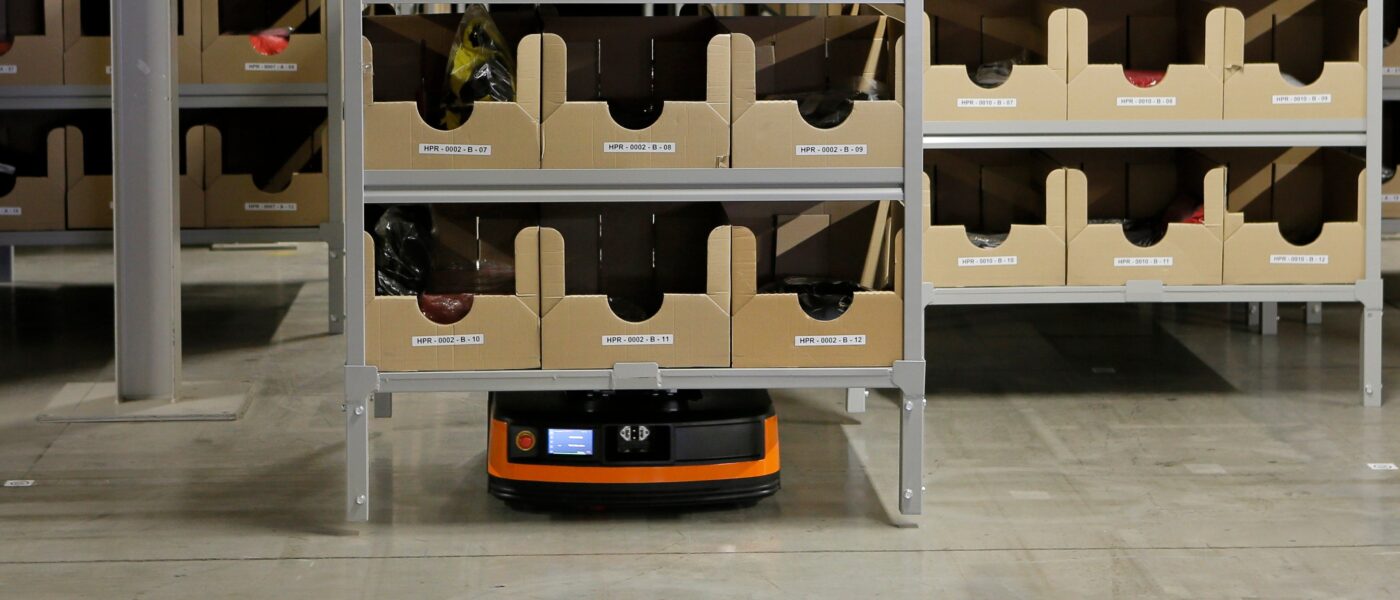
Dec 5th, 2023
Your Warehouse needs GOALS
What are your warehouse goals?
Warehouses always have things to get done. The primary goal often involves some form of picking. Moving items from a general storage area, gathering them into groups that have been selected by client needs or customer orders.
There are other secondary goals too, like re-sorting the storage, or double-checking stock levels, but these are all in service to the primary goal, which is in turn subservient to the overall goal of a business. To be prosperous, profitable, and ultimately to grow. This is where Invar Warehousing Software (IWS) comes in to help.
{% video_player “embed_player” overrideable=False, type=’hsvideo2′, hide_playlist=True, viral_sharing=False, embed_button=False, autoplay=False, hidden_controls=False, loop=False, muted=False, full_width=False, width=’1920′, height=’1080′, player_id=’122683909172′, style=” %}
To achieve all those goals, you need efficiency, accuracy, and cost efficiency, and GOALS are very helpful to get all those things. Not only in the form of strategic targets for your warehouse to achieve and strive for, but also the GOALS that are provided by IWS.
The Grouped Ordering Algorithmic Logistics System (GOALS). A way to ensure your warehouse’s picking processes are as radically efficient as possible.
GOALS is a software system that is powered by artificial intelligence to gather similar orders together as part of the picking process. This means sending pickers on a smaller number of shorter journeys between storage units and means that an individual tote/container/trolley/other mobile sub-storage unit.
To understand it better, here’s an example:
Imagine a grocery warehouse with only six products. Apples, Bananas, Carrots, Dates, Eggs, and Figs.
Now imagine the following orders came in:
Customer #1 – Order arrives at 8:15 AM – 12 Apples, 8 Bananas, 6 Eggs.
Customer #2 – Order arrives at 8:16 AM – 2 Dates, 10 Carrots, 18 Eggs.
Customer #3 – Order arrives at 8:17 AM – 9 Dates, 4 Carrots, 12 Figs.
Customer #4 – Order arrives at 8:17 AM – 10 Eggs, 4 Bananas, 10 Apples
Customer #5 – Order arrives at 8:18 AM – 4 Apples, 9 Eggs, 8 Bananas
Customer #6 – Order arrives at 8:19 AM – 6 Carrots, 4 Eggs, 12 Dates, 7 Bananas.
A system using a standard wave based and time-based ordering system of “first come, first served” might just split these orders into two pickers duties, with a first wave dealing with customers 1, 2, and 3 while a second wave deals with 4, 5, and 6.
However, since customers 1, 4, and 5 all just want Eggs, Apples, and Bananas in varying quantities, it would be faster to group all those orders into one picker’s journey. The same with customers 2 and 6, who only have the very slight difference of 6 wanting bananas also. Customer 3 could also be easily grouped in here too, making the overall routing much quicker.
This is an incredibly simplistic version of what GOALS does. Our modelling here ignores that GOALS also knows how far Figs would be from Eggs, and how many Bananas are remaining currently in storage. However, the underlying principle is clear. Simply dealing with orders as they come in leads to a situation where pickers are roaming the warehouse on journeys that are not just repetitive, but ultimately needless. With a system actively scanning and intelligently grouping your orders, your pickers can be working more efficiently. This saves your warehouse time, gives your customers a better service, and ensures your business has the kind of reputation and reliability it needs to keep growing.
This is the kind of advantage and benefit that IWS offers to your business. Intelligently arranging your operation into an extreme example of achievable efficiency. To discover more about what Invar Warehousing Software is truly capable of, read our latest brochure in full.
{{cta(‘122962365848′,’justifycenter’)}}