Solution
Faster, more efficient packaging systems
Are your despatch operations struggling to cope with rising order volumes? The huge growth in online shopping in recent years has led to far greater volumes of packaged items passing through fulfilment centres. And with tech-savvy consumers accustomed to same- or next-day delivery of their orders, an efficient packing, labelling and despatch process is more critical than ever to the success of your business
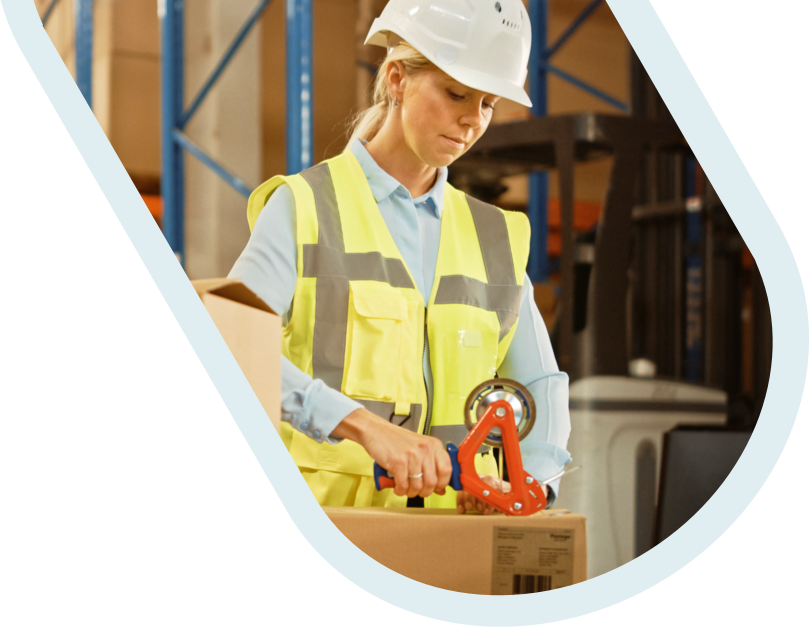
Packing
Eco-performance
Important too, is the consumer’s desire for eco-friendly packaging. We can offer you technology that delivers a better customer ‘unboxing’ experience, with less waste.
Our portfolio of efficient, smart-packing solutions enhances the despatch function of any size of business and, as we are an independent systems integrator, we are not bound by any one technology or in-house manufactured solution. We will design and integrate a system that best suits your needs.
Automated packing technology such as carton erectors, bagging and boxing, sealing and labelling systems can transform your packing operation – boosting throughput and future proofing your business.
Advanced solutions:
- Boxing technology has made great strides, from simple box-erectors and case-sealing machines for improving throughput, to sophisticated fit-to-size automated packing machines that can tailor make up to 1100 boxes per hour.
- Bagging systems available in many formats, from manual machines to fully automated systems – using plastic film or paper – can process many tens of orders per minute.
- Labelling machines for high throughput operations offer reliable performance for packages, bags, and cases – including bar coding and shipping address
Using our powerful, in-house software design capabilities we can deliver the performance gains you are looking for in your packing operations. Automating part or all stages of your packing process has never been more straightforward.
Testimonials