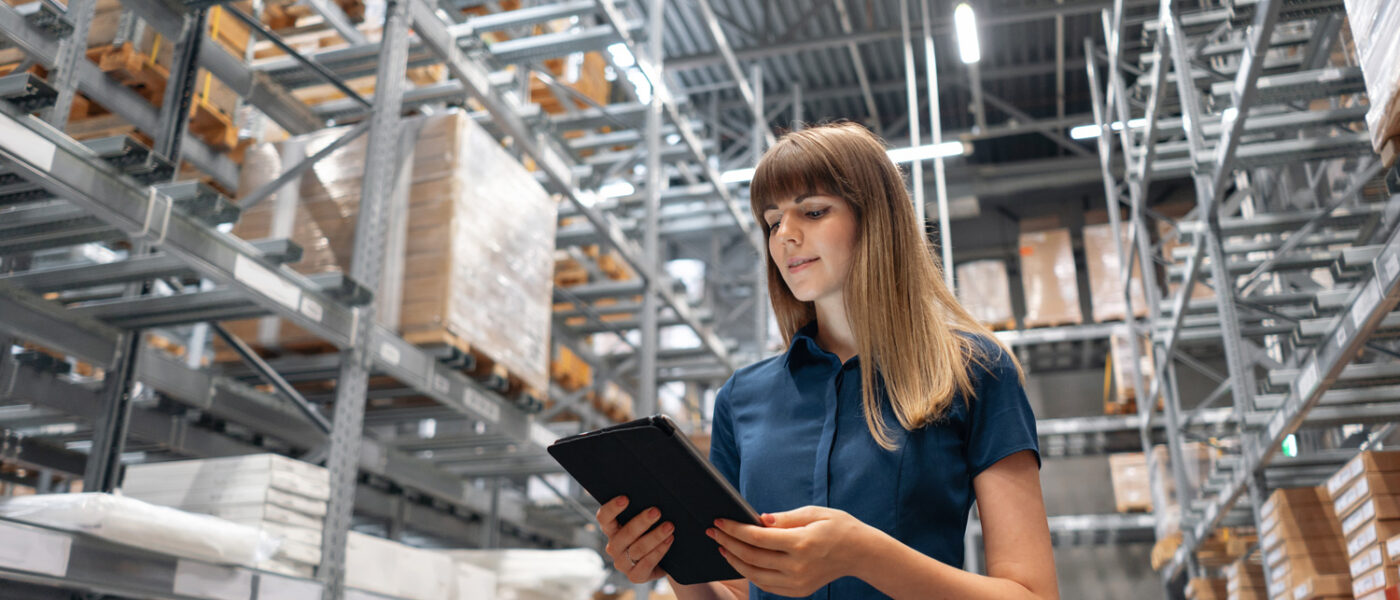
Jan 20th, 2023
Love your warehouse, or list it?
As with the popular TV property show ‘Love it or list it’, many businesses are facing a similar dilemma when it comes to their warehouse. The explosive growth of ecommerce in recent years has radically changed the dynamics of the DC. The emphasis is now firmly on picking, packing and processing small orders consisting of singles or few items – operations that tend to be labour intensive and space hungry.
Unsurprisingly, many are asking: Is our warehouse fit for purpose – is it big enough – should we move? But is size the issue or could automation help businesses love their warehouse again?
List it?
Moving to a larger facility may, on the face of it, sound the most logical option – more space for expanded manual operations. However, modern, hi-spec warehouse space has become a rare commodity in the UK and comes at a hefty premium, along with a commitment to a lengthy lease of 10-15 years.
A report published in January by the British Property Federation and Savills finds that demand for warehouse space across England has been underestimated in planning policy for a decade and that future demand is likely to be at least 29% higher than past levels. This chronic shortage of warehouse space has seen rents rise 61%. Acquiring more space has become an expensive option.
Competition for limited resources extends to the labour market too. Since Brexit, available labour for typical warehousing tasks, such as picking and packing, has become increasingly scarce. In addition, the National Living Wage is rising and also the hike in National Insurance for both employers and employees.
Then there are all the costs and complexity of acquiring a new warehouse, kitting it out and moving inventory and staff. And what of the environmental impact of a move to a larger warehouse – extra heating and lighting costs, more cars in the car park – do they sit comfortably with corporate objectives on sustainability?
Of course, paying for larger premises could be a long-term commitment to what may be an unnecessary expense.
Love it?
The alternative is to make more of the space you already have. Intelligent planning of inventory, together with careful analysis of processes and space, can with the judicious application of appropriate technology, deliver faster throughputs and greater productivity – all within the existing footprint of the warehouse. Well-scoped-out automation has the potential to maximise storage density, boost output, and free-up staff for higher-level tasks, thereby enabling the business to grow by extending the productive life of an existing warehouse.
Low-CapEx technologies, such as Autonomous Mobile Robots (AMRs), provide highly flexible and scalable solutions without all the disruption and rigidity of fixed automation. Using advanced, readily available, goods-to-person picking technology, storage density can be dramatically increased and productivity per picking operative elevated from under 100 to over 500 picks per hour.
Overhead pouch sorters can be a highly productive option in creating dynamic buffering for the quick re-dispatch of fast-selling returned items – all using vacant overhead space.
There are many well-proven technologies that can be brought together by an independent integrator with in-house software capabilities – from weighing and auto volumetric sizing of goods received, intelligent conveyor runs and ASRS systems, to automated packaging machines, sortation equipment and pick-to-light technology, to name but a few.
A clever design concept, brought to life by the efficient integration of smart technologies and intelligent software can turn an existing manual warehouse into a high-throughput fulfilment powerhouse, extending the usefulness of an existing warehouse for years to come.
Who wouldn’t love it?
{{cta(‘5f265ce1-b5d6-494d-9411-e1c3a8db5bd9′,’justifycenter’)}}